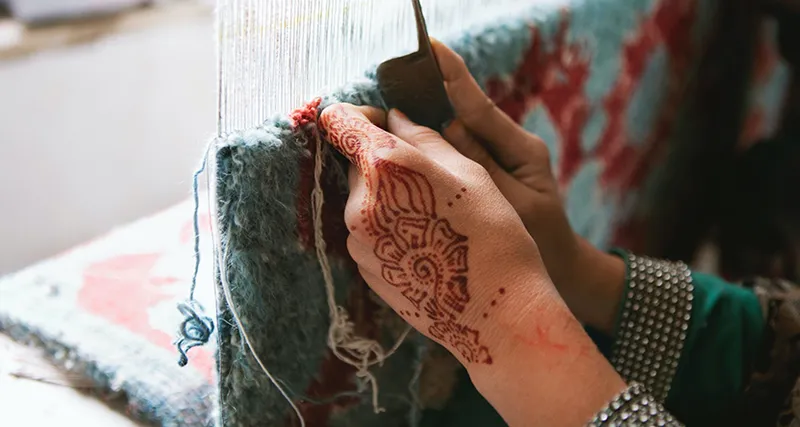
Craftsmanship
Each carpet at Hassan's Carpets is a testament to centuries-old traditions, where skilled artisans weave stories into every thread with meticulous attention to detail.
The Journey To Create A Handmade Rug
Every step of the process, from the first shear to the final finishing carve, is done by hand. Remaining true to our belief in sustainable materials, our rugs are made with the finest natural yarns and dyes. These yarns are then woven in a myriad of ways, creating thoughtful textured designs that are made to last. Explore the extraordinary craftsmanship of this centuries-old tradition with us.

Carding
After the wool has been carefully sheared, it is then hand carded. Carding is the process of disentangling and straightening the jumbled fibres of raw wool by hand, teasing it back and forth between two brush paddles.

Spinning
The hand carded wool or other fibres is fed into a spinning wheel where it is spun and twisted into one continuous long strand of yarn. The experienced weavers produce yarns at various lengths and thickness according to the knot densities required for different designs. After the yarn is spun it is wound around a spool and balled. Hand-spun yarns have a natural irregularity of thickness, which when dyed, is never uniform in colour, creating the charming uneven effect of 'abrash' Mill-spun yarns have more consistency in tension and colouration, resulting in a more even and uniform finishing.

Dyes
Traditionally, natural dyes are produced and acquired naturally through vegetables, plants and minerals such as saffron and walnut shells. Nowadays with the advancements of technology, new engineered dyes are made from other available materials.

Dyeing
After being hand-carded and hand-spun, the yarns are dyed by the Dye Master. The yarns are placed in a large boiler with a boiling mixture of water, dye and binding agent. The yarn is constantly turned on a wheel to ensure that the colour is consistent and has effectively permeated the yarns. However because this is done by hand, the yarns may absorb dyes unevenly - resulting in subtle colour differences in the yarn, known as abrash - this imperfect colour perfections add life and character to the finished rug. Once the dyeing process is complete, the yarn is then left to dry naturally.

Graphs
Graphs show a scaled plan of the overall rug design composition - it is the blueprint for the rug design. Traditionally it was hand painted, but nowadays the graphs are computer generated. The final graph is the template used by the weavers to follow, specifying the colour, material and position of every knot.

Knotting & Weaving
The intricate process of weaving is carried out by skilled artisans working in synchronisation on the loom, guided by the graph that usually sits on the loom in front of them. Handknotted rugs are made on a loom frame, consisting of warp and weft tension threads, which manifests as the foundation of the carpet's structure. The design is then knotted in row by row with the dyed yarns. The higher the knot count density, the finer the rug. There are three commonly used techniques of knotting in handknotted carpets - Tibetan, Persian and Turkish knotting. The Persian method is more traditional, with each knot individually cut by hand to create the pile. The Tibetan technique involves a rod that allows for an entire row of knots to be cut. Handloom rugs are made on a loom with a shuttle. Once the row is complete, the rod is hammered tightly against the row below. The weaver then cuts the yarns along the rod, creating the pile.

Washing
Washing is an essential step in rug production, not only does it ensure that the dyes are colour fast and have truly binded to the yarn; it also enhances the softness of the pile, sheen and colours. The rugs are thoroughly washed on both sides with soap and water using a wooden paddle called 'pharwa; that combs through and squeezes out water and dirt from the pile.

Stretching
Handmade rugs aren't straight when they come off the loom. Once washed, they are taken for stretching. The stretching process will make the rug as perfect and straight as possible. The rug is outlined and stitched on a metal or wooden frame where it stays for a few days to make sure the rug is aligned.

Drying
The rug is then dried on roof terraces or in and around open spaces surrounding the washing area. They leave the rug an extra 2 days in the sunlight as this further enhances the sheen and lustrous look.

Shearing
Once dry, the rug is laid flat and the pile cut and shaved neatly to the required height by hand with a shearing machine. This can be quite a tricky process as the exact same pressure should be applied everywhere so the pile height is identical all over the rug.

Clipping & Carving
During this finishing process, pattern elements are carefully carved out and contoured by hand with scissors, giving definition and three dimensional effects to the rug's design. This extraordinary intricate detailing is done by a team of talented craftsmen. (Enhances the texture and tunes up the look)

Binding
The final stage involves neatly wrapping the sides of the rug in a yarn that matches the design. The rug is then ready for its new home.